 |
 |
|
 |
|
 |
|
 |
|
 |
|
|
 |
|
 |
|
 |
|
|
|
Posted on August 27, 2012:
Back at it again!!! This episode I am working on the piston which is made from a solid piece of bar stock. The Red Wing kit includes a 1.5 diameter piece of class 30 gray cast iron of which the piston is to be made out of (seen below). This type of cast iron is a graphitic alloy which makes it easy to machine and resistant to wear due to the lubricating effect of the added graphite.
|
|
|
 |
|
|
The Red Wing engine is designed to have a compression ratio of around 5.25 : 1 which computes to about .450-.460 head space (distance from TDC piston to head). Since the engine has a few variables including crank location and cylinder length I must verify that the piston will end up in the .452 range. To do this I will measure the distance between the wrist pin center and the bottom of the head. I can then subtract 1.060 (the piston height up from the wrist pin) to get my head space measurement. I used my calipers to see where Top Dead Center (TDC) puts the wrist pin the bore (seen below). I measured 1.706 plus half the diameter of the wrist pin (.156) to come up with 1.862 to the top of the cylinder. Since the head protrudes into the bore .370 (with head gasket) I can subtract that amount from 1.862 to come up with 1.492 (wrist pin center to the head).
|
|
|
 |
|
|
The drawings show the piston as 1.060 from the wrist pin to the top of the piston so I can subtract this amount from 1.492 to get .432 which is .020 too close to the head. For this reason I will be shortening the piston about .020 to lower the compression ratio into specification (.452). Note: The engine will probably run fine without compensating for head space however I wish to be as exact as I can to report my findings on how well the suggested compression ratio works. Before moving on I calculated my new compression ratio using a .452 headspace value. I added .02 cu in for the spark plug hole and the compression release bore to the total volume to get my new compression ratio of 5.266 : 1 (which is plenty close enough). Note: Total displacement is 2.454 cu in or 40.214 cc.
|
|
|
 |
|
|
The first step is to machine a face on one side. This will be the bottom of the piston.
|
|
|
 |
|
|
The next step is to bore a 1/2 hole 1.5 deep into the rod.
|
|
|
 |
|
|
I used my new boring bar to shave out the recess inside the skirt.
|
|
|
 |
|
|
I cut the recess at 1.050 diameter by .3 deep...
|
|
|
 |
|
|
I custom ground a 1/4 tool bit with a .060 radius for the next cut.
|
|
|
 |
|
|
I cut the recess about .075 deeper while rounding off the inside corner for a total depth of .375 as seen below. I also widened the diameter to 1.063 as the prints show.
|
|
|
 |
|
|
I cut a 45° bevel into the inside edge at 1/32 wide...
|
|
|
 |
|
|
I removed the piston from the lathe and used my round stock center square to scribe a horizontal alignment line on the bottom as seen below. This will help orient the piston on the next few steps.
|
|
|
 |
|
|
Using the alignment line I was able to orient the piston on a set of V-blocks to drill out the wrist pin holes. I used a square to visually line up the marks as seen below.
|
|
|
 |
|
|
The next step is to center the spindle over the piston. For this I used a round stock center finder tool (seen below).
|
|
|
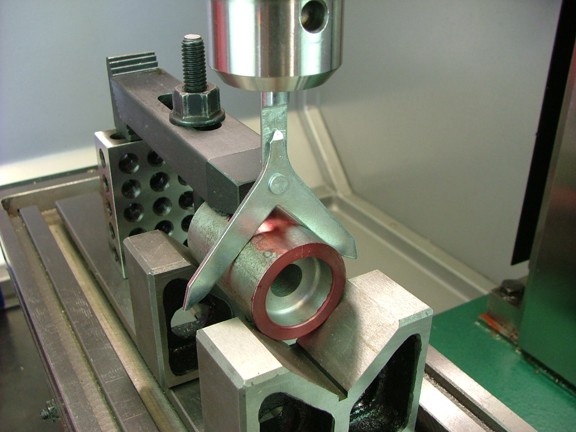 |
|
|
I now used my wiggler tool to set up the spindle at the bottom of the skirt and zero out the table.
|
|
|
 |
|
|
The next step is to move the spindle .690 up from the bottom and spot the wrist pin hole with a #2 center drill.
|
|
|
 |
|
|
A 9/32 drill was used to drill straight through the piston.
|
|
|
 |
|
|
I now used a 5/16 oversized (+.001) chucking reamer to ream out the wrist pin hole. I oversized the hole to allow for a slip fit of the wrist pin.
|
|
|
 |
|
|
The next step is to roll the piston horizontally for the oiler hole. I used a parallel to sight in the alignment as seen below.
|
|
|
 |
|
|
I now spotted the oil port hole with a #1 center drill Using the same measurement of .690 up from the skirt (not shown). I then chased the hole with a 3/32 drill bit into the center of the piston.
|
|
|
 |
|
|
The next step is to orient the pistons horizontal alignment marks to the travel of the table. I did this with the wiggler tool. This is in preparation for milling out the connecting rod pocket.
|
|
|
 |
|
|
I then found the center of the skirt recess and zeroed out the table...
|
|
|
 |
|
|
I mounted up a 1/4 end mill in a collet (to ensure accuracy) and zeroed out the spindle depth (Z axis) indicator at the bottom of the skirt (top edge). Note: I will be using X, Y and Z coordinates to indicate where my spindle will be located over the milling table for each step. The negative values of the X and Y axes will be at the upper left corner of the table and the positive values will be to the lower right (personal preference). This means that if the table is traveling left (spindle right relative to table) the X value is positive and if the table travels up or away from the operator (spindle down) the Y value is positive. The Z axis is positive as the spindle is raised. I like this style of coordinates as it is much like reading where you always start from the upper left corner and work your way down. It is also easy to remember that when you spin the tables handwheels clockwise you are traveling in a positive direction...
|
|
|
 |
|
|
Using the hand wheels on my table I located the first plunge cut to be made at -.300 in the Y axis (X= 0,Y= -.300) from the center of the piston (seen below). This first plunge cut was made to a depth of .900 (Z= -.900).
|
|
|
 |
|
|
The next cut was made at .115 to the left (spindle travel) on the X axis or X= -.115,Y= -.300.
|
|
|
 |
|
|
I followed up with a series of cuts including a mirrored cut at +.115 from the center line (X= +.115, Y= -.300). I then moved on to two more plunge cuts at X= +.115, Y= -.200 and X= -.115, Y= -.200 for a total of five cuts on the back end of the pocket (seen below). All of the cuts were made to a depth of .900 from the bottom of the skirt.
|
|
|
 |
|
|
I mirrored the process on the front side of the pocket at the following coordinates:
|
|
X= 0 Y= +.300 X= -.115, Y= +.300 X= +.115, Y= +.300 X= +.115, Y= +.200 X= -.115, Y= +.200 Z= -.900
|
|
|
 |
|
|
I now used the 1/4 end mill to widen the pocket. I moved the spindle out to -.126 on the X axis (from center) and -.312 on the Y axis and plunge cut to a depth of 1 (Z= -1). I then milled out my first pass toward the coordinates of X= +.126, Y= -.312. I then moved the cutter to X= +.126, Y= +.312 for my second pass, X= -.126, Y= +.312 for my third and X= -.126, Y= -.312 for my last pass.
|
|
|
 |
|
|
The next step is to drill out the wrist pin set screw holes. I moved the table out to X= -.375, Y= 0 and then spotted one of the holes with a #1 center drill. I also spotted the other side using X= +.375, Y= 0 (not shown).
|
|
|
 |
|
|
I now drilled out both sides with a #43 drill bit as seen below.
|
|
|
 |
|
|
A 4-40 tap was used to thread out the wrist pin set screw holes at this time...
|
|
|
 |
|
|
For the most part the complicated work is now complete and I can move on to the final OD of the piston.
|
|
|
 |
|
|
I set up the piston in my three-jaw chuck and supported the skirt end with a bull nose live center. This will ensure the piston will not shift in the chuck and that I can access all of the pistons outer surface with a tool bit.
|
|
|
 |
|
|
I set up a indexable tool bit holder with a diamond shaped carbide insert to cut down the OD of the piston. I used a feed rate of .007 IPR (Inches Per Revolution) at an RPM of 180 for these cuts. I made most of my passes at a depth of .010 which seemed to cut the best.
|
|
|
 |
|
|
The grey cast material cut very nicely even over the wrist pin holes...
|
|
|
 |
|
|
Once I got closer to my final OD of 1.2485 I tapered down my depth to .001 cuts to be sure not to ruin my piston. The finish at this point is perfect and looks much like a modern forged piston. The very slight corrugation of the tool bits cut will help retain lubricating oil and thus reduce friction so there will be no further finishing.
|
|
|
 |
|
|
I double checked my dimensions with the micrometer and was ready to move on to the ring grooves.
|
|
|
 |
|
|
To lay out my ring grooves I must consider that my piston will be .020 shorter than on the prints (to correct the compression ratio). The prints show the top groove at being 1.625 from the top edge of the groove to the bottom of the skirt. I shortened this dimension to 1.605 and used my calipers to scribe out the first line using the lathe. I then made marks at 1.511, 1.417, 1.323, 1.229 and 1.135 for all three ring grooves. At this point I had noticed that the oil ring groove (third groove from the top) was just as wide as the two compression ring grooves. The O-ring that fits into this groove is much narrower that the slot provided for it. I was tempted to custom fit the groove to the O-ring but then it dawned on me that the gap was intentional. The O-ring needs to have some play to mop up the oil on the cylinder wall and hold it in this channel (or at least that is my theory ;0).
|
|
|
 |
|
|
I started cutting the first groove with my .085 wide carbide parting tool to a depth of .0743 from the surface (1.1 diameter). I then widened the first groove to the required .094 width.
|
|
|
 |
|
|
I locked down the carriage and used my compound rests graduated wheel to help me verify the correct location of each groove. I then used my calipers to gauge the width of each groove to specification.
|
|
|
 |
|
|
I cut the third and final groove to finish up the process....
|
|
|
 |
|
|
I very slightly beveled the edges of the lands with a needle file (with the lathe turning slowly) so that no material will come loose later on (not shown).
|
|
|
 |
|
|
And now for the moment of truth!!! I test fit the piston in the cylinder and was overjoyed with a beautiful fit :0) The piston slides silky smooth into the bore with about .0005 clearance. Note The prints suggest a .0015 clearance however I expect that break-in wear will create the extra .001 within the first few minutes of running. We will have to wait and see ;0)
|
|
|
 |
|
|
The next step is to cut off the machining head of the piston. I mounted the piston in the three-jaw chuck protecting it with a layer of blue tape. I then slowly started removing material from the top of the piston as seen below.
|
|
|
 |
|
|
Once I got closer to my final piston height of 1.730 (prints call for 1.750) I slowed down and made .005 cuts to the final dimension.
|
|
|
 |
|
|
I double checked the height of the piston as well as the desired thickness of the top land to the top of the piston (.125). I was good to go :0)
|
|
|
 |
|
|
I used an X-Acto knife to bevel out the wrist pin holes and then moved the piston over to the mill to bevel the oil port hole in the top side. This was done with a #2 center drill...
|
|
|
 |
|
|
At last the piston is complete!!!
|
|
|
 |
|
|
I am very happy with the final results.
|
|
|
 |
|
|
I finished the day with a quick fit check of the piston down the cylinder. Needless to say I am impressed with the accuracy of my new machines. Having the right tools sure makes a difference ;0)
|
|
|
 |
|
|
Well I cant be any more enthused to finish this build. I really am having so much fun with my new equipment and I am already looking for the next project ;0) Please join me again for the next installment of the Red Wing Project!!!!
Till then be safe my friends!!!
Don R. Giandomenico
|
|
|
 |
|
 |
|
 |
|